Measurement of the scaly patches
Scaly patches - Transverse or rounded recesses on the surface of the roller, formed due to uneven solidification of the weld pool metal.
Scales are measured for neighboring scales using their maximum height difference
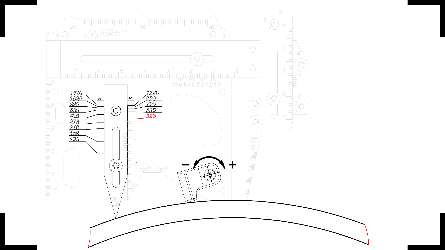
positioning the welding gauge
- Set the welding gauge at the zero position
- Pull the fillet arm 2 out of the main gauge plate 1, matching the mark with a value corresponding to the diameter of the pipe being monitored
- Fix and lock the stop position by tightening the fillet arm rivet 6.
- Position the welding gauge on the test object perpendicular to the weld and close to the fusion line..
- After rearranging the pivots in the groove located on the right side of the welding gauge, adjust them until they come into contact with the inspected object.
- Lock the pivots in this position as shown by the illustration
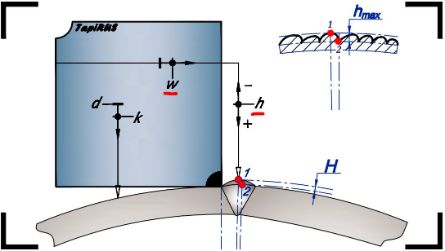
˟ the parameter measured during the monitoring process is highlighted in red
measurement taking
- т. 1 Move the linear member 3 so that the taper gauge 5 is above the measurement point, lower the top High-Lo arm 4 until the taper gauge 5 makes contact with the surface of the weld joint.
- For т. 1, take the value of the parameter w from the horizontal scale W, and subsequently the readings of the parameter h from the vertical scale H.
- Having shifted the welding gauge along the seam, measure the parameters w and h for the adjacent flake - T. 2 as shown.
- To obtain the desired parameter H shown in Figure 43 use a calculator, to find the values of h ' in т. 1 and т. 2. and measure their difference.